One-Stop Metal Custom Welding Parts Factory Since 1993
Get Factory Price Start From 100pcs
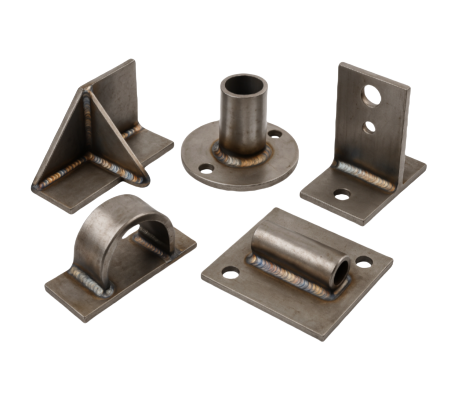
With over 30 years of experience, our large-scale production ensures you receive high-quality parts at cost-effective prices.
Take advantage of our 100pcs minimum order, helping you reduce costs while maximizing your business's profitability.
All of our products are ISO certified and adhere to strict quality standards, ensuring reliability and safety for your industrial needs.
Provide revolutionary custom metal parts for your industry
Customized metal weldments can be divided into several main types according to the processing technology, each process has its unique characteristics and application fields. The following are some common types of metal weldments grouped by process and their characteristics and areas of application:
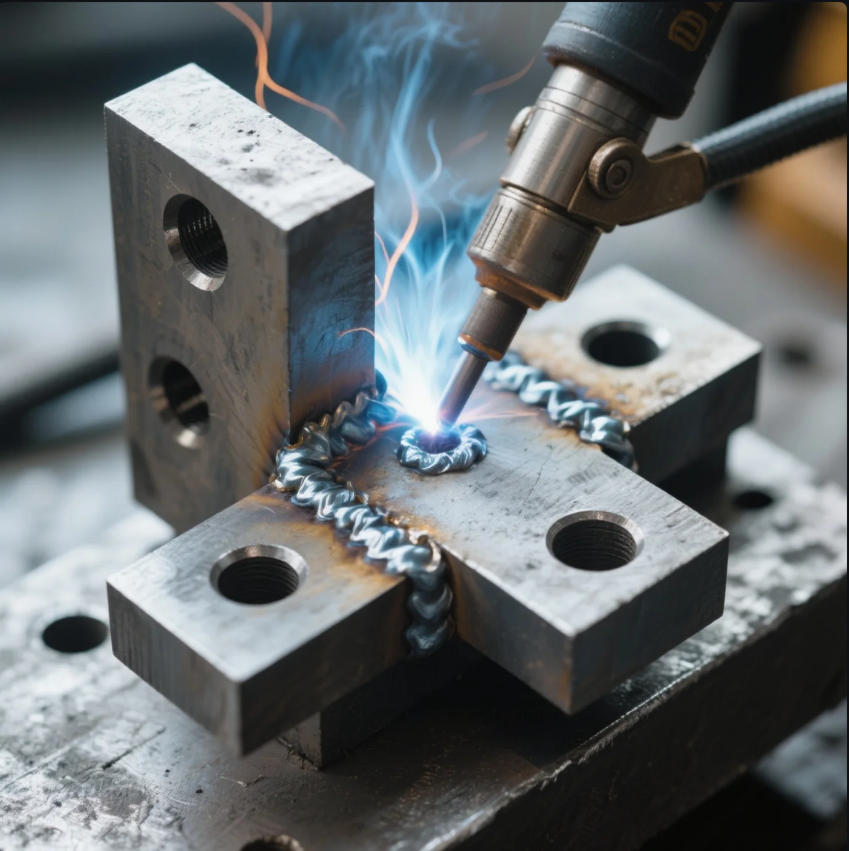
ARC Welding
Features:
- ARC welding is the process by which the arc heats the metal, causing it to melt and join.
- Fast welding speed, wide range of applications, suitable for most metal materials (such as steel, aluminum, etc.) .
- The utility model can be used for welding large thickness metal, and the welded joint has high strength.
Applications:
- Construction industry: steel structure, bridge, building frame, etc. .
- Automotive industry: Automotive chassis, body structure, engine brackets and so on.
- Shipbuilding: hull construction, cabins, etc. .
- Machinery and equipment: large mechanical frame and supporting parts.
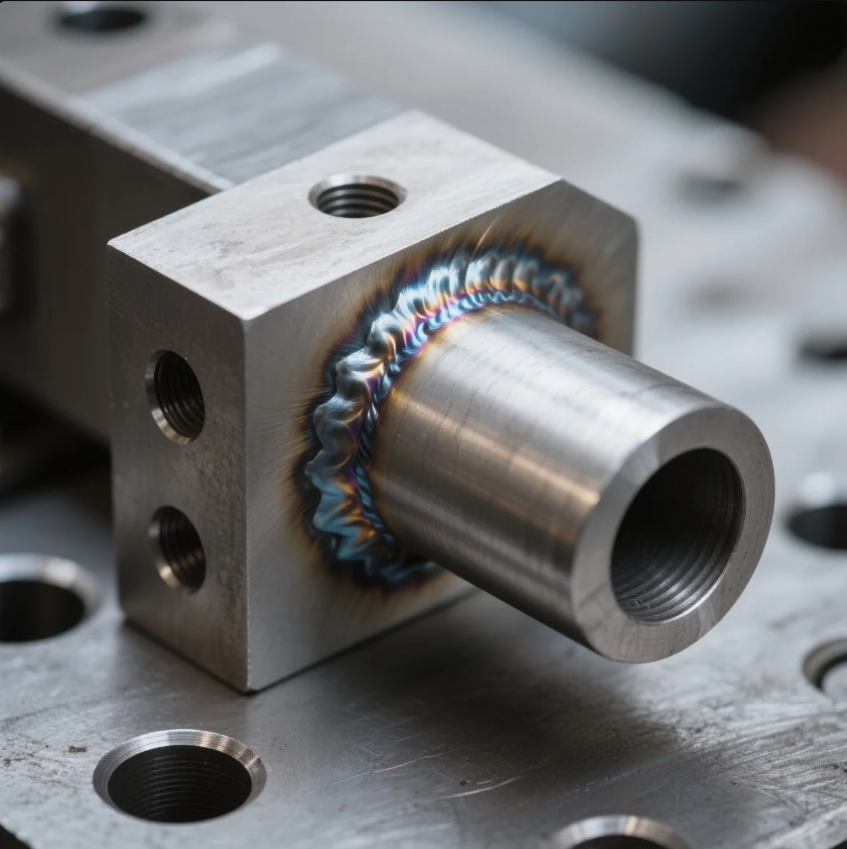
TIG Welding
Features:
- Argon arc welding uses inert gas to shield the welding area to ensure that the metal is not oxidized.
- High welding quality, smooth weld, small heat affected zone, suitable for fine welding of thin metal materials.
- Welding process control precision, suitable for precision parts manufacturing.
Applications:
- Aerospace: aircraft structure, engine parts.
- Automotive industry: high-precision body welding, engine parts.
- Precision Instruments: electronic equipment shell, precision instrument bracket.
- Medical Equipment: medical instruments, surgical instruments, etc. .
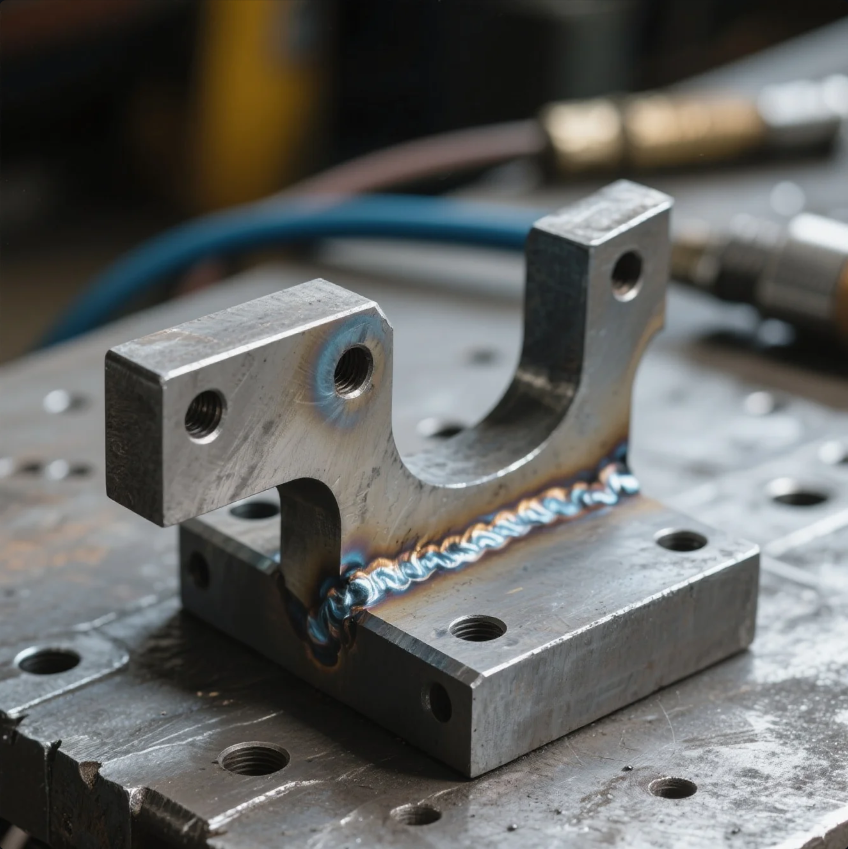
MIG Welding
Features:
- MIG welding uses an arc to heat the wire and substrate, while shielding gases such as argon and carbon dioxide are used to avoid oxidation.
- Fast welding speed, easy operation, good welding quality, suitable for medium and thick plate materials.
- High strength welded joints for high efficiency mass production.
Applications:
- Automobile Manufacturing: welding of automobile body and chassis.
- Shipbuilding: Hull Construction and large welded parts.
- Heavy Machinery: excavators, cranes and other heavy machinery frame.
- Furniture Manufacturing: metal furniture, decorations, etc. .
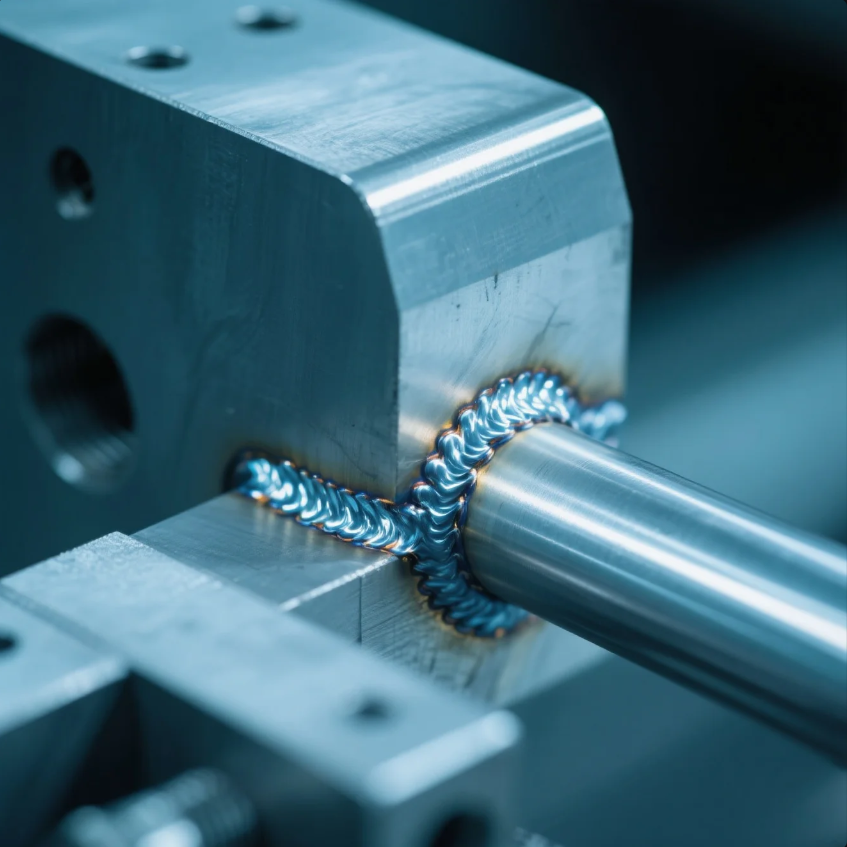
Laser Welding
Features:
- Laser welding uses a high-power laser beam to focus on the metal surface, quickly heating the metal and melting it to form a welded joint.
- Welding precision is extremely high, heat affected zone is very small, welding speed is fast.
- Suitable for precision, thin material welding, welding seam clean, smooth.
Applications:
- Electronics industry: mobile phone case, computer accessories, LED lamps and so on.
- Automotive industry: body precision welding, sensors and other small parts.
- Medical industry: high-precision medical instruments, endoscopes, etc. .
- Photovoltaic industry: solar cell modules, photovoltaic panels.
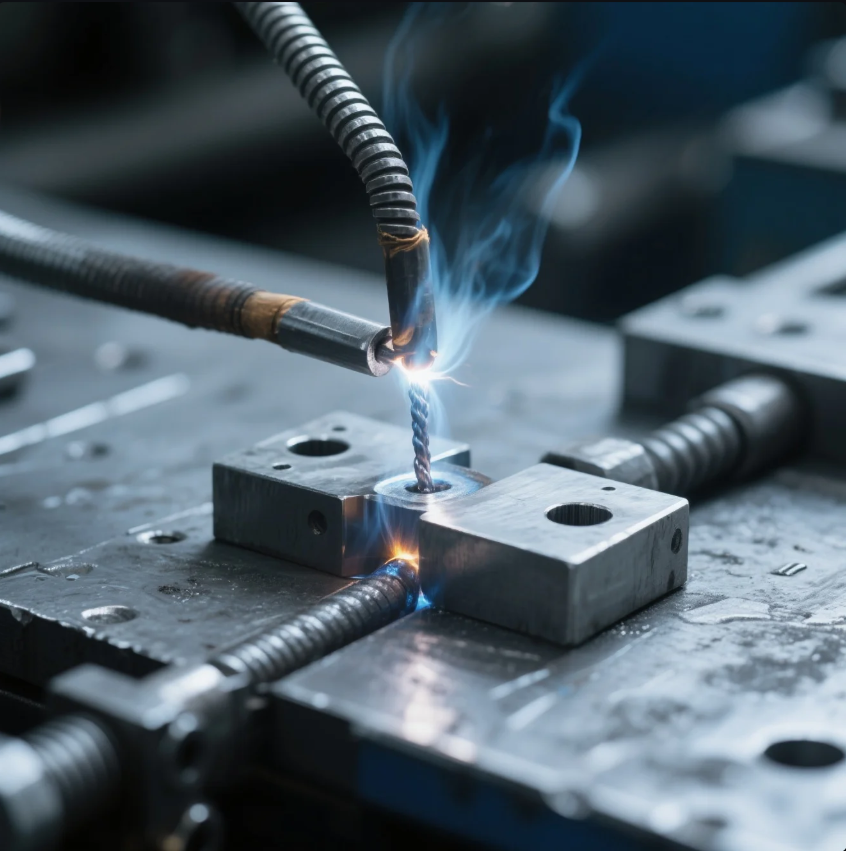
Spot Welding
Features:
- Spot welding is a local welding process, mainly through the electrode pressure and current, so that the local heating of metal to molten state, the formation of welding points.
- Welding speed is very fast, suitable for mass, rapid mass production.
- Less heat input, suitable for welding thin plate materials.
Applications:
- Automotive industry: spot welding body connection, such as doors, roof and bottom, etc. .
- Home appliance industry: Spot Welding Connection of electric appliance shell.
- Electronics: small batteries, electronic component connections, etc. .
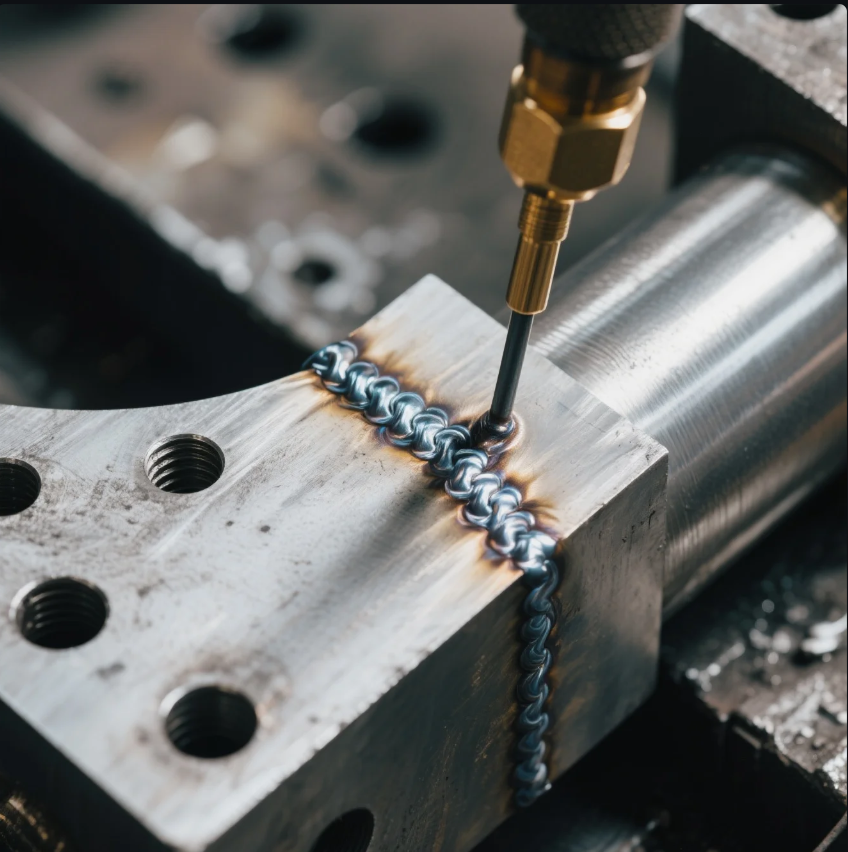
Gas Tungsten Arc Welding (GTAW)
Features:
- Similar to conventional TIG welding, it employs a non-consumable tungsten electrode, utilizes argon gas as a shielding gas during welding, and provides precise welding control.
- High welding strength and smooth weld seams make it suitable for the production of precision components.
- Due to its high precision, it is commonly used in the welding of high-value-added products.
Applications:
- Aerospace: welding of aircraft engine parts.
- Nuclear Industry: Welding of nuclear reactor components.
- High-end mechanical manufacturing: welding of high-precision mechanical components.
Who we are
Professional welding service is ready to cooperate.
- High-precision welding: Using advanced welding technology to ensure the dimensional accuracy and surface quality of each product.
- Customized services: according to customer needs, to provide different specifications, materials and customized welding parts.
- Durable:The selection of high-quality raw materials to ensure that the product has extremely high mechanical properties and service life.
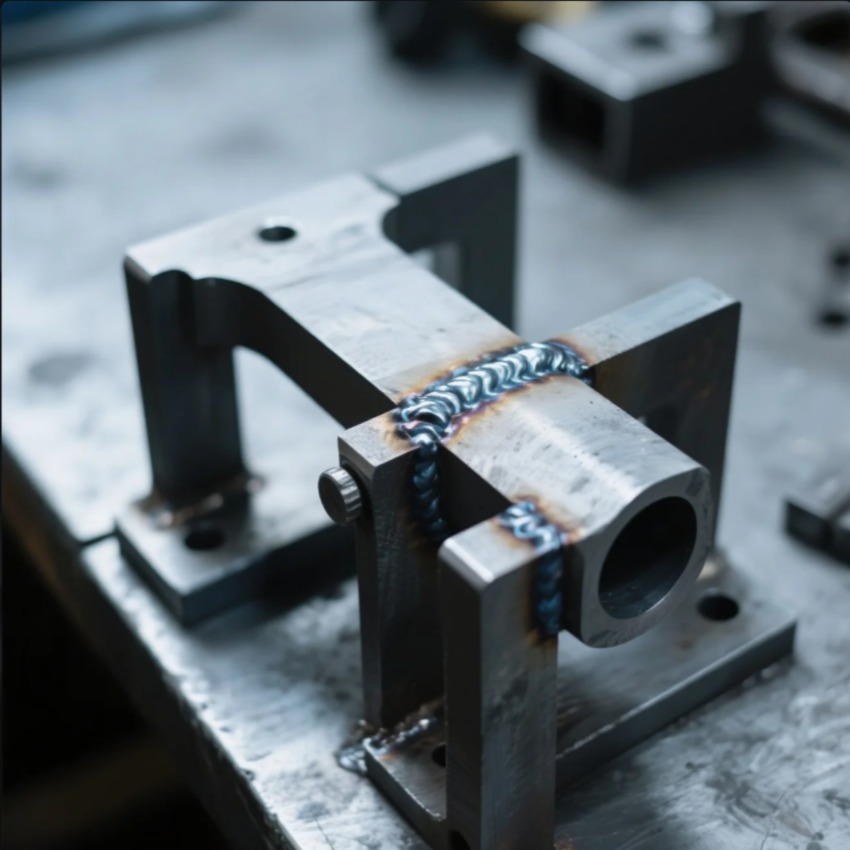
We are committed to helping you achieve your goals with reliable custom hardware solutions.
What Sets Us Apart
We offer a wide variety of custom metal parts to meet your needs and budget.
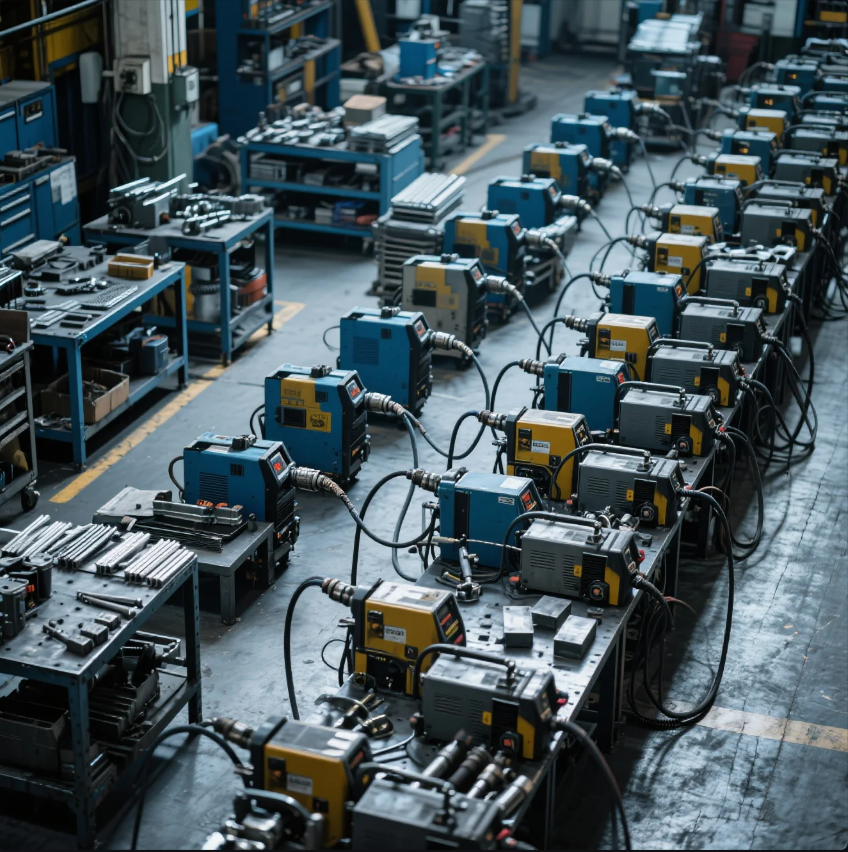
Well-Equipped Facility
We are equipped with fully automatic production lines, as well as specialized mold manufacturing and deep processing workshop.Can provide high-precision production for your products.
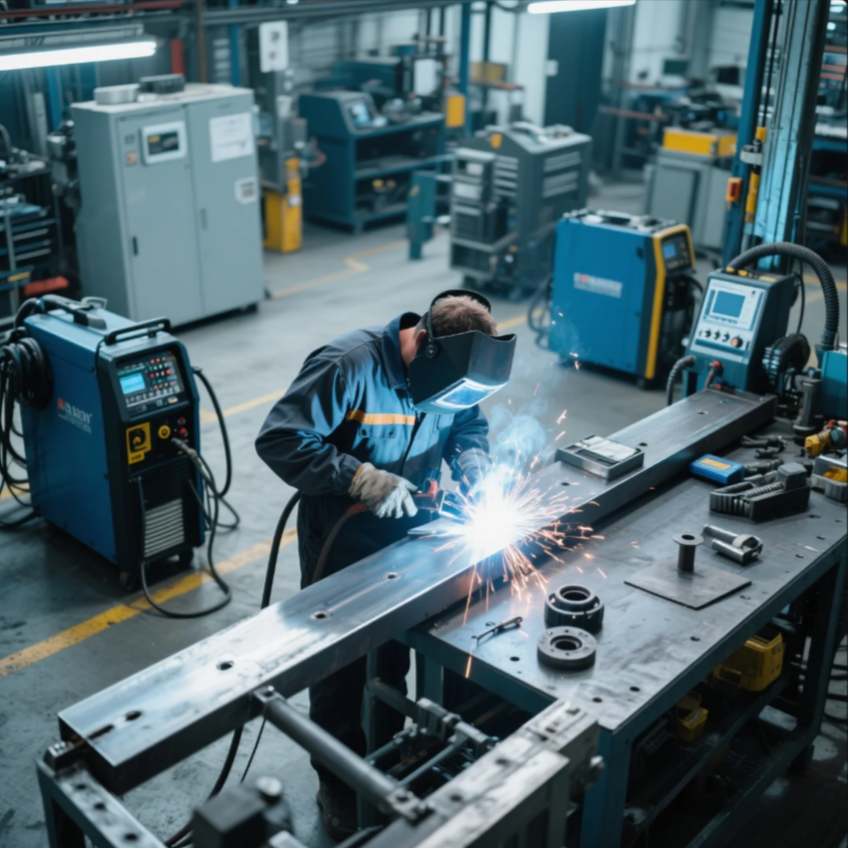
Advanced Manufacturing Capabilities
We are equipped with multiple welding production lines, our advanced machines can ensure the highest efficiency, improve your production efficiency.
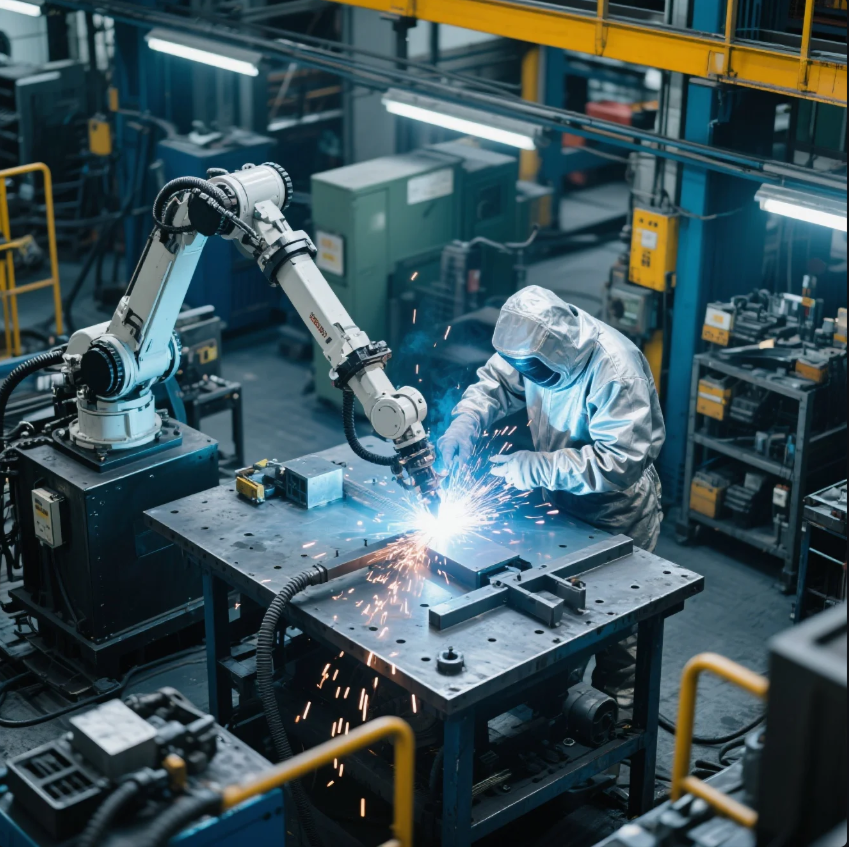
Competitive Pricing
Through bulk orders and a stable supply chain, as well as our streamlined manufacturing process, we can save the cost of raw materials to provide you with very competitive pricing.
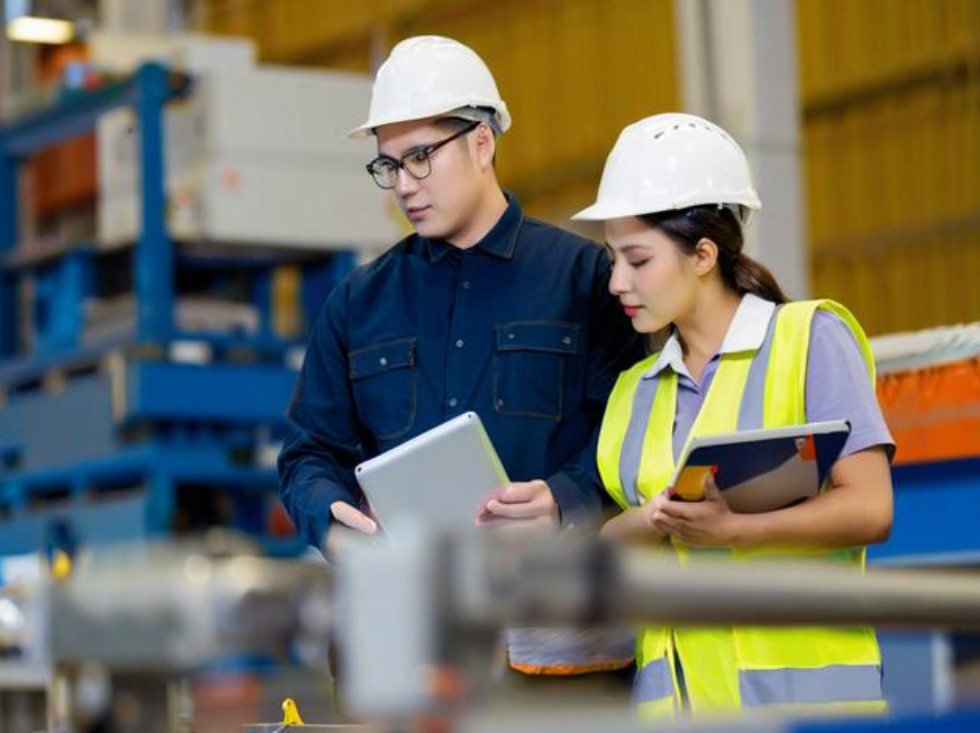
Comprehensive Support & Services
From pre-sales consultations to manufacturing and after-sales care, we deliver tailored solutions based on your design requirements, with a guaranteed quote within 24 hours.
The Process Flow & Duration Estimation
The production process of metal welding parts requires precise process control and high-level technology to ensure that the welding parts meet quality standards and meet the special requirements of customers. The following are the main steps in the production of metal weldments:
Step 1: Design and drawing validation
Before production, the engineer will provide the design plan and technical drawing of the welding parts according to the customer’s requirements and design requirements. Design drawings including welding size, shape, material requirements, as well as welding process selection. Ensure that the design conforms to the feasibility of production, and after customer confirmation to the next step.
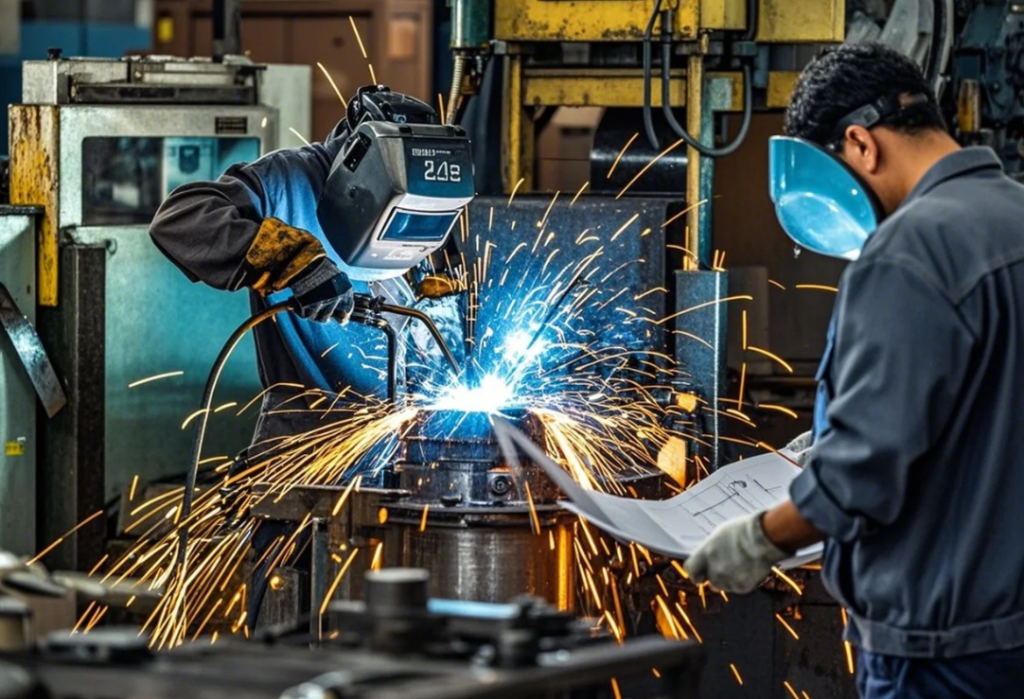
Step 2: Preparation of materials
According to the design drawings and process requirements, select the appropriate metal materials (such as steel, aluminum, stainless steel, etc.) . In this step, the material is pre-inspected to ensure that its quality meets welding requirements. In addition, the selected materials also need to be cleaned to remove surface dirt, grease, oxides, etc. , to ensure the smooth progress of welding.
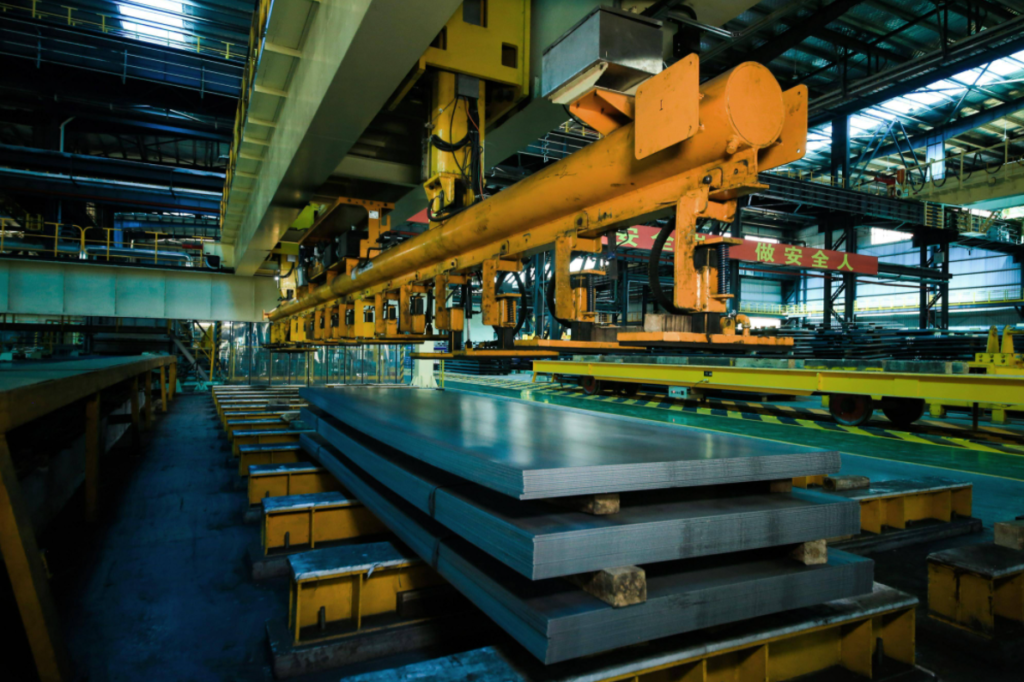
Step 3: Cutting and machining of workpieces
The metal material is cut to a shape and size suitable for welding according to the design dimensions. Common cutting methods include laser cutting, plasma cutting, shearing, etc. . After cutting the metal parts usually need further processing, such as grinding, deburring, etc. , to ensure the accurate size of the workpiece and good welding contact surface.
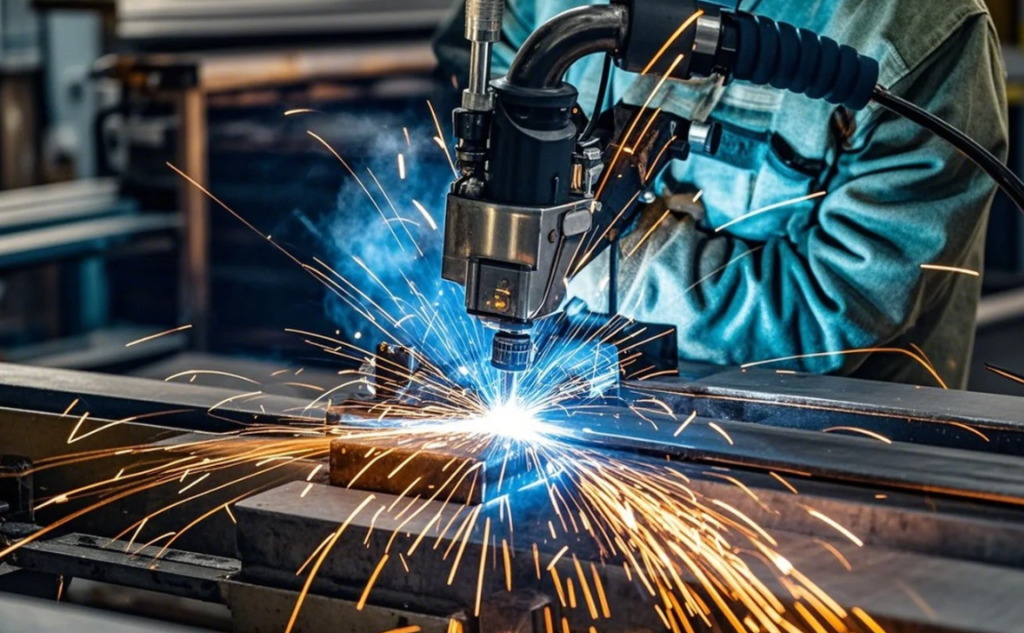
Step 4: Prepare for welding
Before welding, the welding area needs to be inspected and prepared. First of all, check the fit of the welding workpiece, to ensure that the fitting accuracy of the joint part to meet the requirements. Then, according to the selected welding process (such as arc welding, argon arc welding, MIG welding, etc.) , prepare the appropriate welding materials and shielding gas. Make sure the equipment is debugged and the welding environment is in accordance with the safety standard.
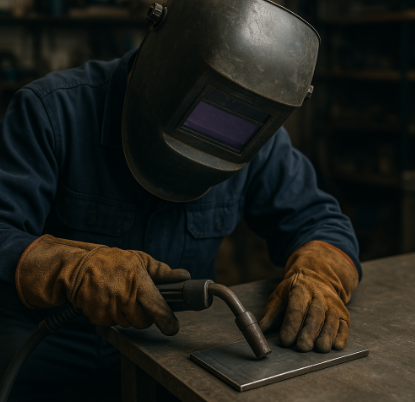
Step 5: Welding operation
Cleaning and deburring: after the casting is removed, there may be excess metal or burrs on the surface, which need to be cleaned by grinding, sandblasting, etc. .
Welding Process Control: to ensure that the welding heat input, molten pool size, welding speed, etc. in line with technological requirements.
Welding Monitoring and adjustment: real-time monitoring of welding in the welding process, if there is a problem can be adjusted at any time process parameters.
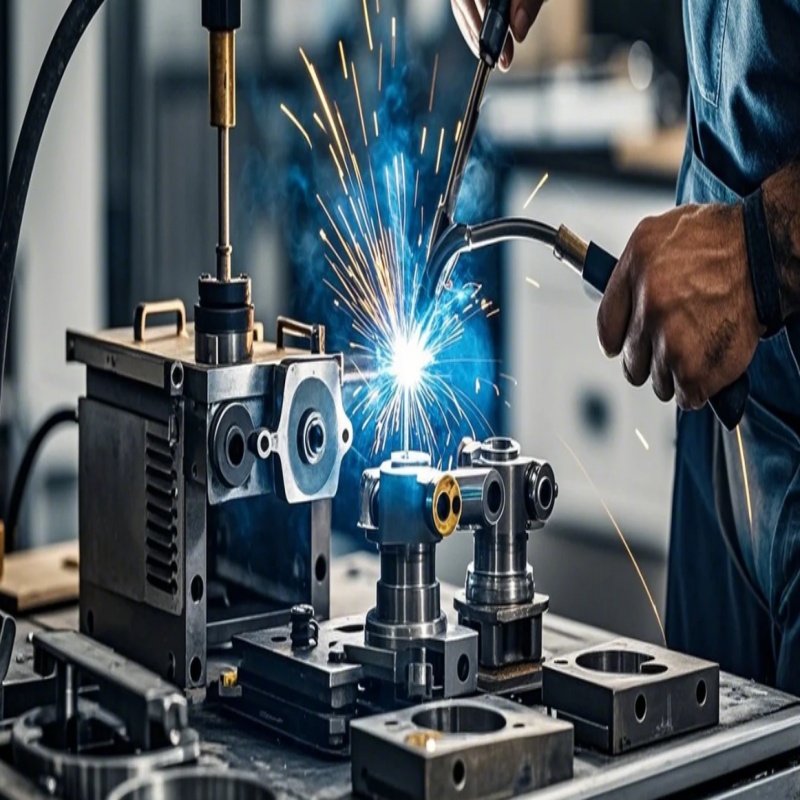
Step 6: Post treatment of welding
After the welding is completed, the welded joint needs to be post-treated to remove the residues and oxides generated during the welding process to ensure the strength and appearance of the welded parts. Common post-processing methods include:
- Weld cleaning: use brush, sandpaper and other tools to clean the weld slag around the weld.
- Deoxidation: the use of chemical or mechanical methods to remove oxides in the welding area to prevent corrosion.
- Heat treatment: some welded metal parts may need heat treatment, such as annealing, normalizing, etc. , to eliminate stress and improve strength.
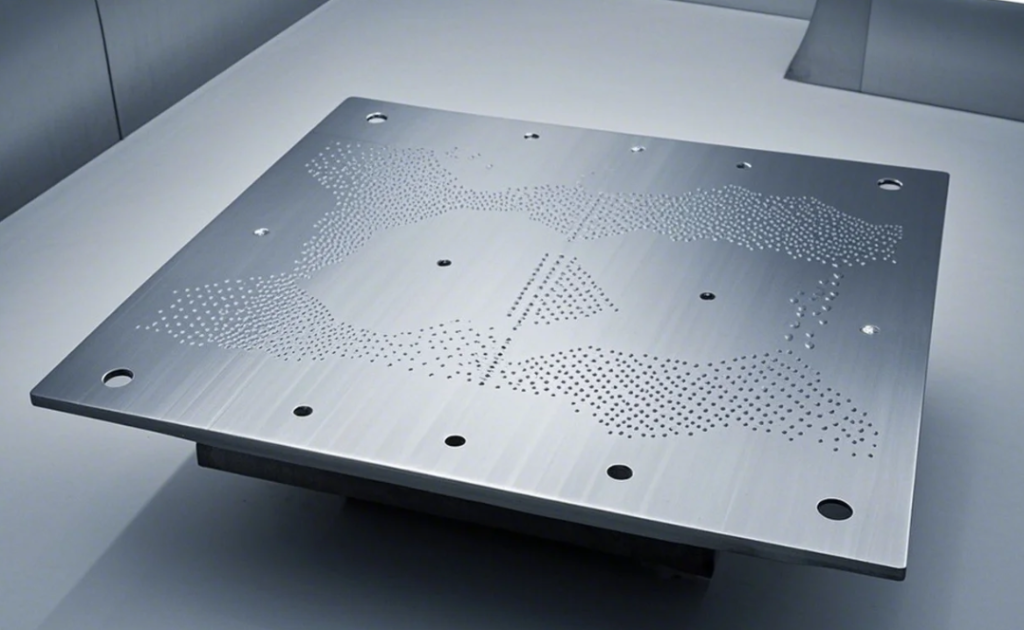
Step 7: Quality inspection
After welding, the metal parts need to go through strict quality inspection to ensure that each product is in accordance with the design standards. The testing items include:
- Dimensional inspection: ensure that the dimensions and shape of the weldment are in accordance with the design drawings.
- Weld inspection: through visual inspection, ultrasonic testing, X-ray inspection and other methods to detect the existence of weld porosity, cracks, lack of penetration and other defects.
- Strength test: tensile, bending and other physical properties of welded parts are tested to ensure that its strength and bearing capacity meet the requirements.
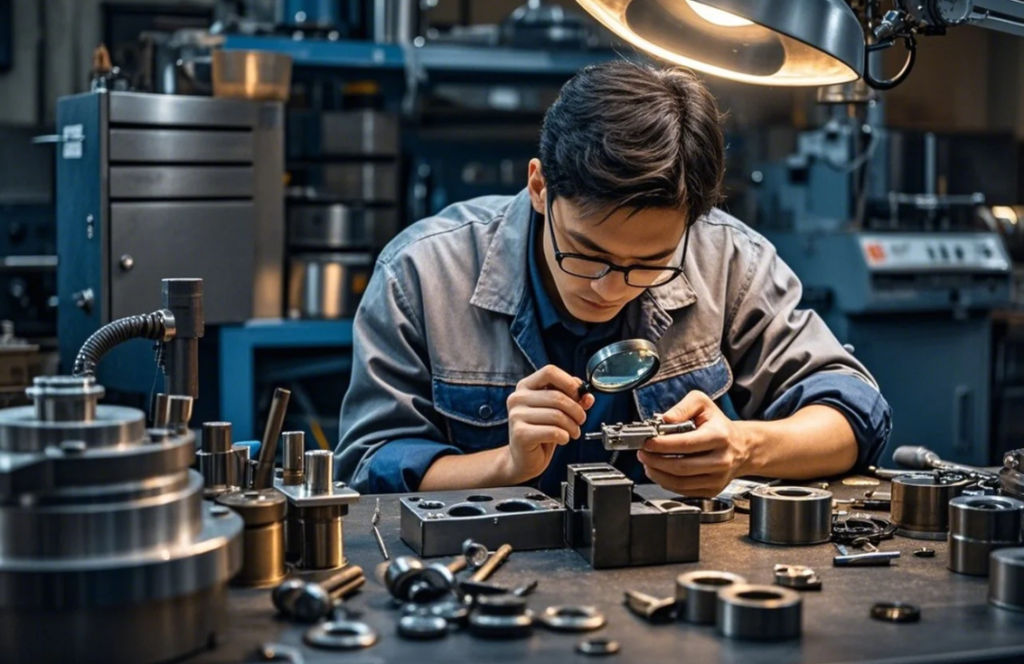
Step 8: Packaging and shipping
After quality inspection of qualified welding parts into the final packaging link. According to the customer’s requirements and product characteristics, select the appropriate packaging, to prevent damage during transportation. Packaged products will be shipped according to the order arrangement to ensure timely delivery to customers.
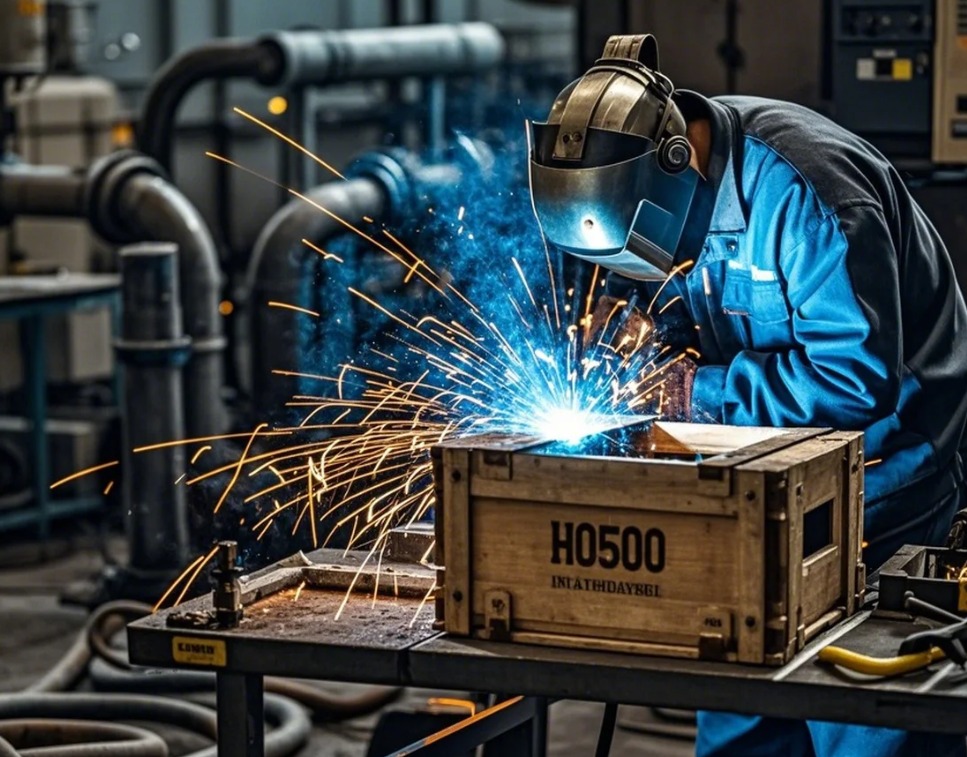
Step 9: Delivery of finished product:
Upon completion of all inspection and post-processing, the castings will become the final product, ready to be delivered to the customer or used for assembly.
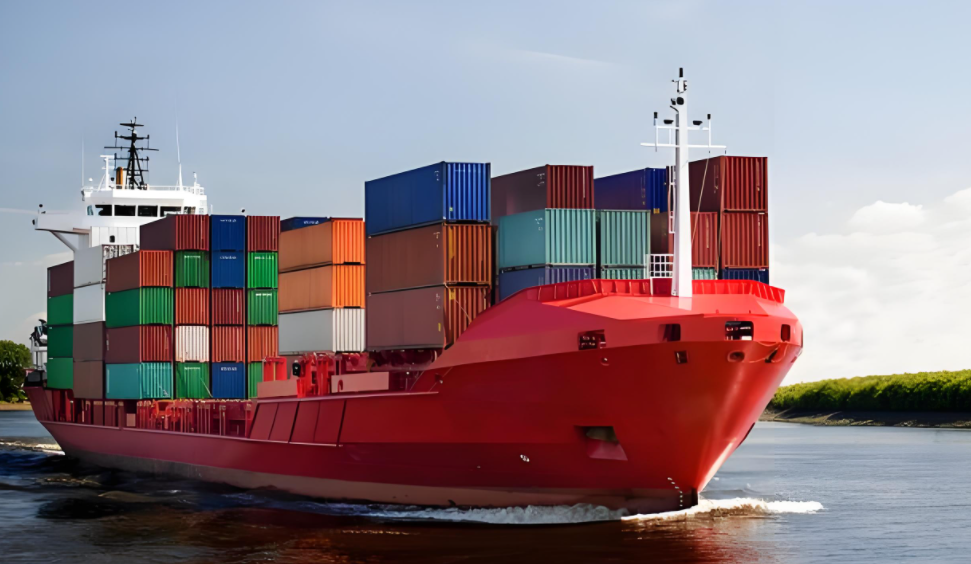
Apllications
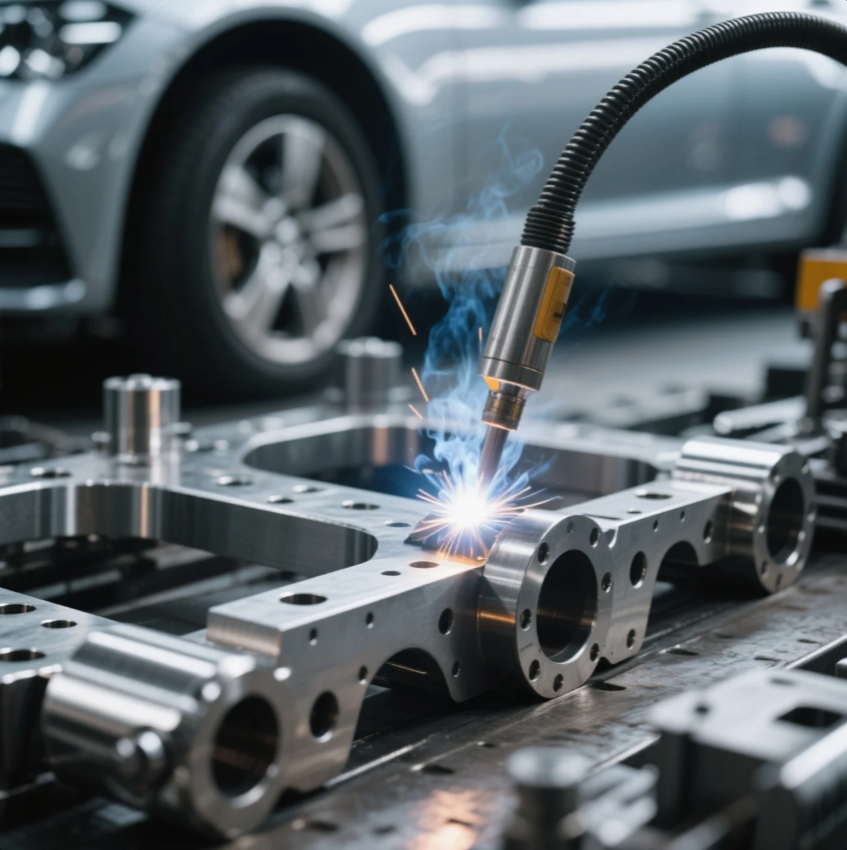
Automotive Industry
Application:Frame, chassis components, exhaust system, SEAT Bracket, safety and anti-collision structure, etc. .
Features:There are strict requirements for the strength, fatigue performance and lightweight of welded parts
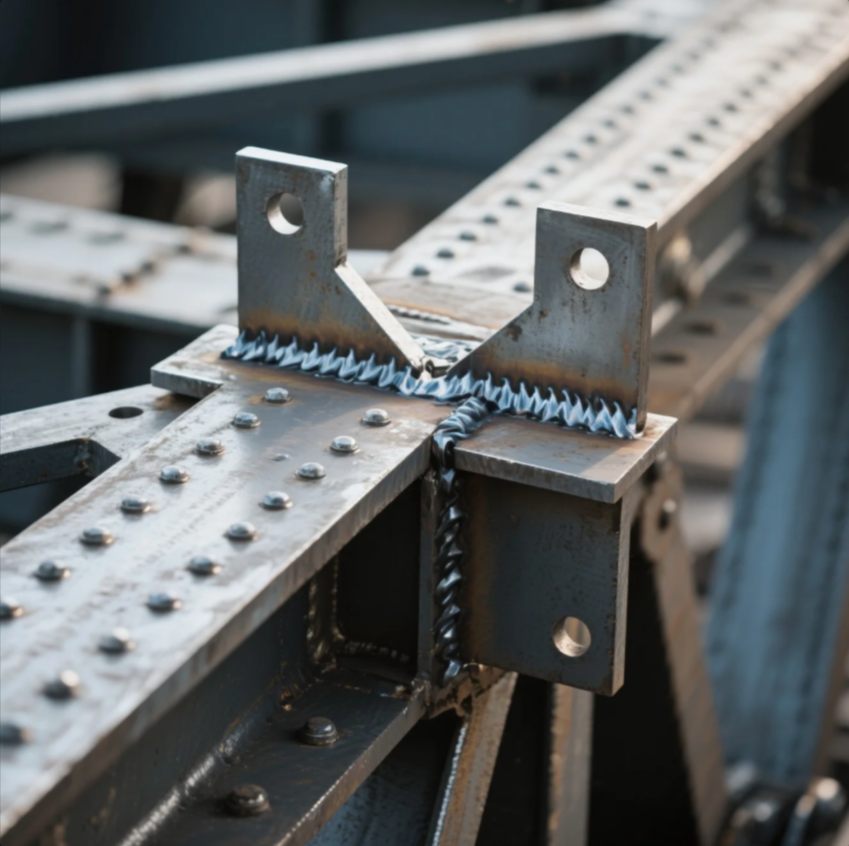
Construction & Structural Steel
Applications:Building steel frame, bridge components, railings, curtain wall support system, scaffold connectors, etc. .
Features:The welding parts have large volume and strong bearing capacity
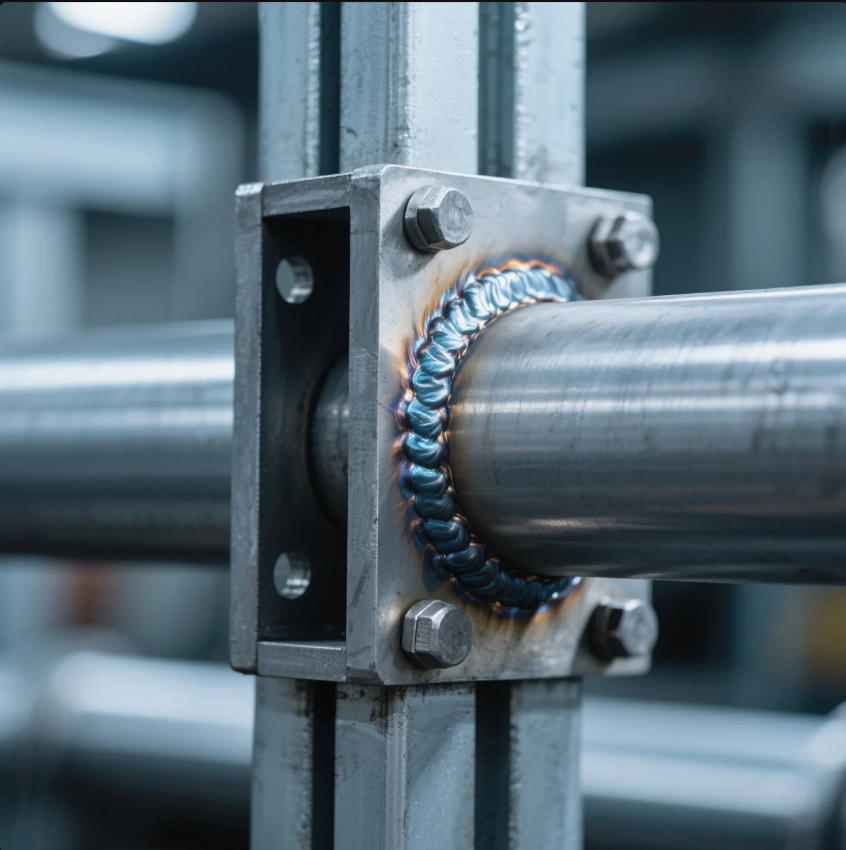
Machinery & Equipment Manufacturing
Applications:Frame, boom, transmission shell, hydraulic cylinder, equipment support frame, etc. .
Features:Commonly used thick plate welding, welding process and deformation control requirements are high
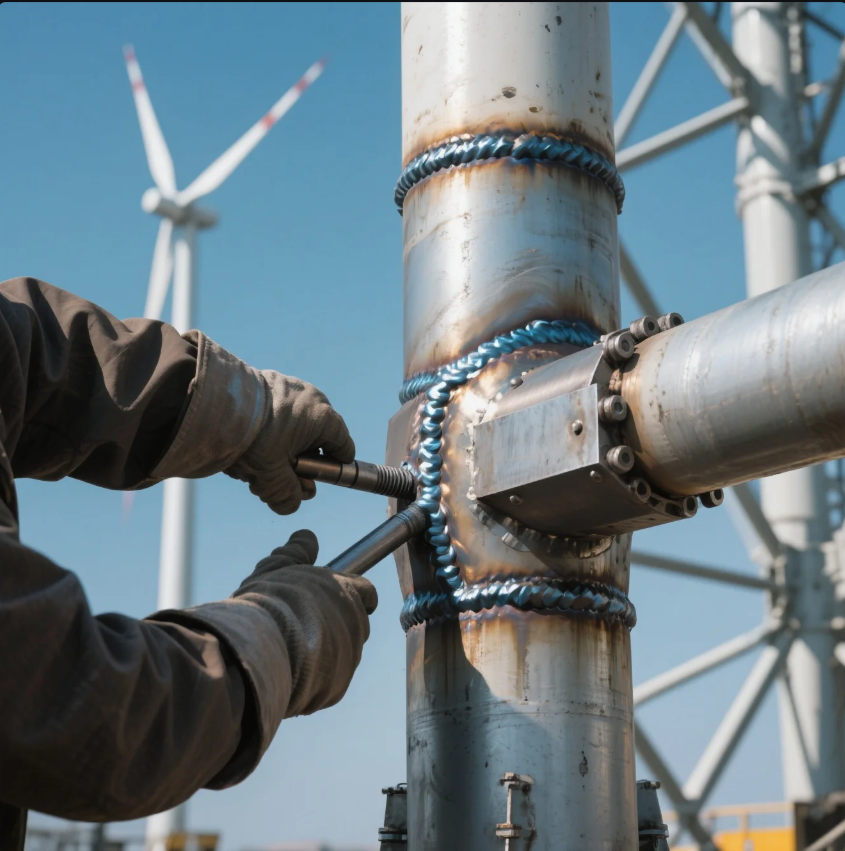
Energy & Power Industry
Applications:Wind power tower, solar energy bracket, boiler and pressure vessel, cable bracket, etc. .
Features:Welding parts should be resistant to high temperature, high pressure or harsh outdoor environment
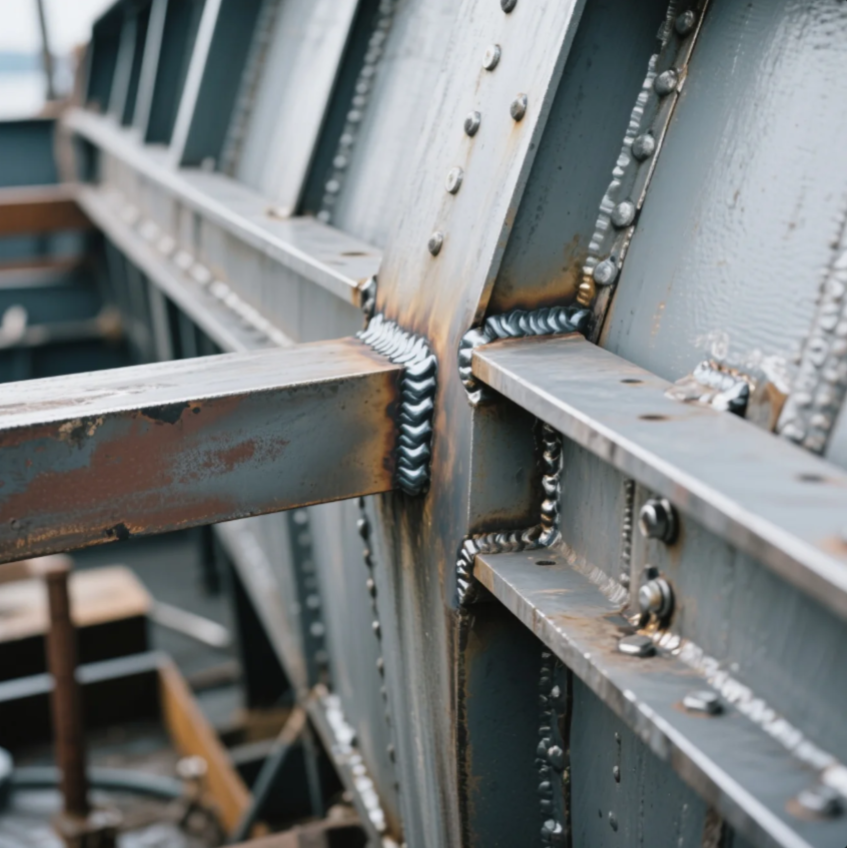
Shipbuilding & Offshore Engineering
Applications:Hull structure, bulkheads, support beams, offshore platform structural parts, etc. .
Features:The welding workload is large, and the requirements for weld continuity and anti-corrosion are high
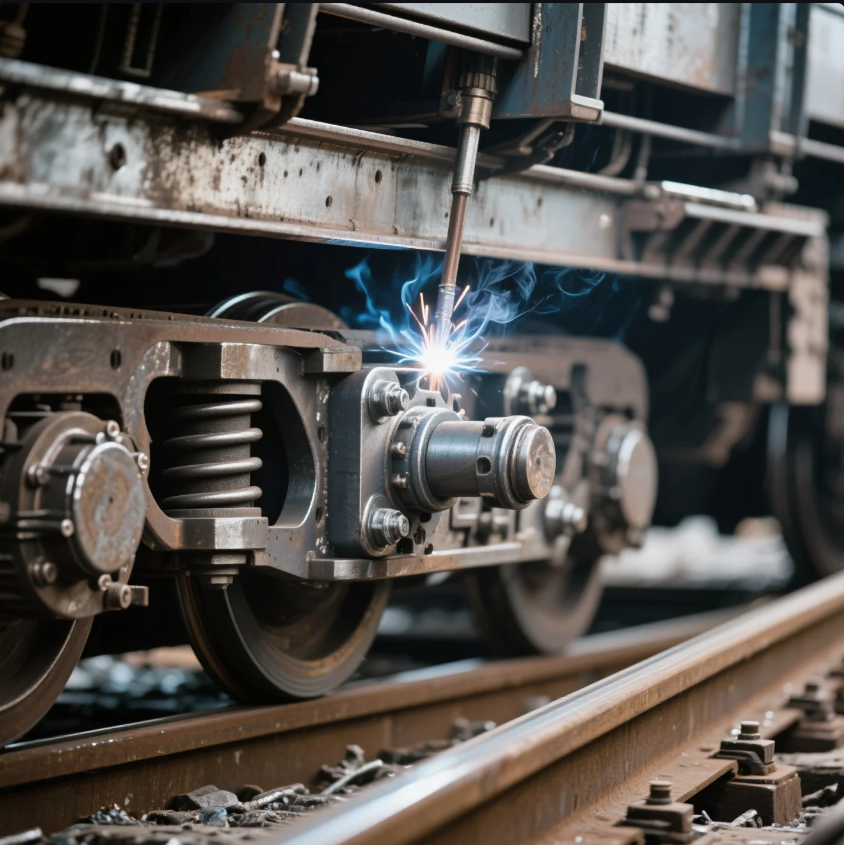
Rail Transit
Applications:Train body, chassis, door frame, connecting members, etc. .
Features:Requirements of beautiful structure, Weld often need to be polished
Why Choose Us
Our promise is in our quality.
Our Happy Clinets
Frequently Asked Questions
Is there a problem? If you can not find the answer here, please feel free to contact our professional team.
How do you ensure the quality of hardware parts purchased from Prime?
At Prime, we prioritize quality by adhering to strict quality control measures throughout the production process. Our products are manufactured in accordance with ISO standards, ensuring consistency and reliability. We also offer sample testing to ensure the products meet your exact specifications before mass production, so you can be confident in the quality of your order.
Are Prime's customized hardware parts competitively priced?
Prime offers highly competitive pricing through efficient production processes and effective supply chain management. By optimizing these areas, we keep costs low without compromising quality. We provide personalized quotes based on your order size and specific requirements, ensuring you receive the best value for your investment.
Can Prime meet delivery deadlines?
Yes, Prime has extensive experience in international logistics, ensuring that orders are delivered on time. We work closely with you to develop a detailed production and shipping schedule tailored to your timeline. If you have urgent needs, we also offer expedited services to guarantee timely delivery and meet your business demands.
What kind of after-sales support does Prime offer?
Prime offers comprehensive after-sales support to ensure customer satisfaction. If there are any issues with the products after delivery, our customer service team is available to address your concerns and provide timely solutions. We maintain clear communication throughout the process to ensure a smooth and satisfactory experience for you.
How does Prime handle shipping and packaging?
Prime ensures that all products are securely packaged to prevent damage during transit. We use high-quality packaging materials tailored to the size and nature of the products. For large orders or specialized items, we offer customized packaging solutions to safeguard the products and ensure they arrive in perfect condition.
What customization options does Prime offer for hardware parts?
Prime specializes in providing tailored solutions to meet your specific needs. Whether it’s custom dimensions, materials, or special functionality, our engineering team works closely with you to bring your design to life. Share your requirements with us, and we’ll provide the best possible customization options to suit your project.
Get in touch
Easily customize metal parts
Share detailed information about your needs, including drawings, reference images, and any specific ideas or specifications you have in mind.
Based on your requirements and design, we’ll provide a custom solution and send you a detailed quote within 24 hours.
Once you approve the design and quote, we’ll begin mass production and take care of the shipping, ensuring timely delivery.
Get a Free Quote
Please contact us for free quotes and expert advice on your requirements for custom metal parts. At Prime, we will provide the right solution for your project, ensuring quality and accuracy at every step to meet your needs and budget.